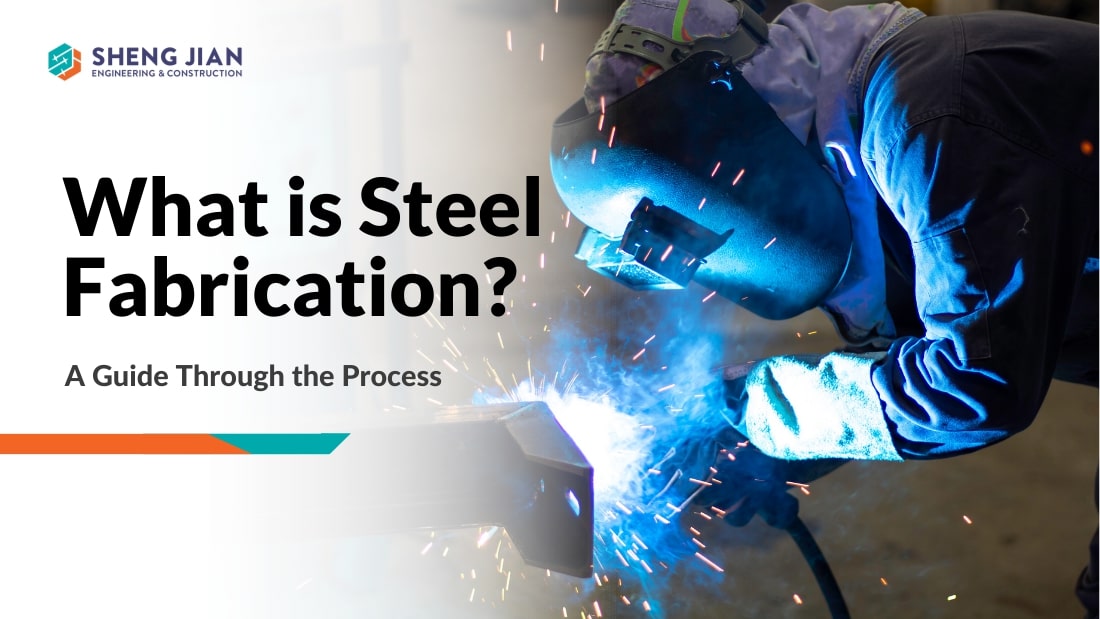
24 Apr What Is Steel Fabrication? Process & Applications Explained
Steel fabrication is the backbone of modern infrastructure, forming the structures that support industrial plants and factories, to buildings and skyscrapers. But what is steel fabrication, exactly?
In this guide, we’ll be covering the process of fabricating steel and its common applications, along with why choosing the right steel fabrication company is crucial for the success of any industrial or commercial project.
Understanding steel fabrication
Steel fabrication is the process of transforming raw steel into pre-defined shapes and structures. It involves cutting, bending, assembling, and welding steel parts according to project specifications.
In industries like oil and gas, automotive, and construction, structural steel fabrication is a core component for building frameworks, support systems, pipework, and storage solutions that are safe, compliant, and long-lasting.

Steel fabrication turns raw steel into core construction or assembly components
The steel fabrication process: Step-by-step
Here’s how steel goes from raw material to high-performance component:
1. Design and detailing
The fabrication journey starts with detailed engineering drawings and 3D CAD models. These take exact measurements, material grades, and structural load data into account. Accurate detailing at this stage simulates and analyses the structure’s performance, ensuring smoother coordination with other trades during installation.
2. Material selection
Depending on structural requirements and project environment, materials are selected based on strength, corrosion resistance, weldability, and cost.
For example, marine or chemical environments may leverage stainless steel, while industrial framing might use mild steel. There are also alloy steels for applications requiring enhanced strength or high-temperature resistance.
3. Cutting and shaping
Precision cutting is crucial. Tools like CNC plasma cutters, laser cutters, and oxy-fuel torches are used to cut raw steel sheets or plates into specific shapes. This step lays the groundwork for seamless assembly later and reduces material waste when done correctly.
4. Bending and forming
Steel may need to be curved, angled, or formed into complex geometries.
Press brakes and roll forming machines are used to apply calculated force to create desired bends while maintaining structural integrity. Accurate forming ensures components fit together precisely during assembly.
5. Assembly and welding
This is where individual parts become a whole. Welders join components using MIG, TIG, or arc welding techniques, depending on material type and structural load.
During this stage, teams align, clamp, and weld parts according to the design drawings, ensuring dimensional accuracy and structural continuity before final inspection.
6. Surface treatment
After assembly, steel components undergo surface finishing to protect against rust, chemical exposure, or high-heat environments. Methods like sandblasting, hot-dip galvanising, powder coating, or epoxy painting are applied to meet specific durability requirements or aesthetic preferences.
7. Quality inspection and delivery
Before dispatch, all components are inspected for dimensional accuracy, weld strength, and surface treatment integrity. Non-destructive testing (NDT), such as ultrasonic or magnetic particle testing, may be conducted.
Once approved, the finished steel is packed, labelled, and prepared for shipment to the installation site.
Applications of structural steel fabrication
Fabricated steel components are used in almost every industrial sector. Common applications include:
- Factory buildings and warehouses
- Equipment skids and pipe racks
- Industrial platforms and walkways
- Steel tanks and silos
- Bridges, towers, and structural frames
- Despite different settings, these applications rely on steel’s strength and reliability for various uses, be it supporting heavy machinery or creating safe walkways, making structural steel fabrication essential in modern industry.
Work with a contractor you can trust
Steel fabrication doesn’t just affect individual components — it shapes your project’s timeline, cost, and long-term reliability. Working with the right partner helps you meet technical standards, avoid delays, and reduce maintenance risks over time.
If you’re looking for a dependable steel fabrication company in Malaysia, SJEC has over two decades of experience delivering safe, high-quality steelwork across industries. From structural steel to storage tanks and bulk material handling, our in-house expertise ensures every solution is built to perform.
Contact us today to discuss your structural steel needs and get a quote!
FAQ
What is meant by steel fabrication?
Steel fabrication is the process of cutting, shaping, assembling, and treating raw steel into finished parts used in construction, manufacturing, and industrial projects. This process transforms steel into materials for specific requirements.
Why is steel fabrication important?
Steel fabrication enables the creation of durable, high-strength components essential for building safe and efficient infrastructure. These pre-engineered solutions allow for customisation, precision, efficiency, and cost savings in large-scale builds.
What is the difference between steel manufacturing and steel fabrication?
Steel manufacturing involves producing steel from raw materials like iron ore, typically in large-scale steel mills. On the other hand, steel fabrication processes manufactured steel into customised parts or structures for use in industries such as construction, oil & gas, and logistics.
What is the most common steel for fabrication?
Mild steel (also known as low-carbon steel) is most commonly used due to its excellent weldability, ductility, and cost-effectiveness. It’s ideal for structural frameworks, industrial equipment, and general construction applications.